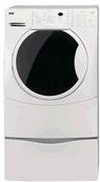
Now I'm not even remotely handy but after some searching online I found some instructions that looked easy enough even for an all thumbs handyman like me.
This blog/post is meant to summarize what I've found and also provide you with step by step instructions with photos to help you save the $500 or so it would cost for the parts and labor Sears would charge you to repair your washer.
Follow these instructions and in 2-3 hours of work and roughly $40-50 of materials you'll have a working washer again, free of the dreaded F11 error code. For full size pics in new windows click any of the pics below.
I realize some of my terms aren't going to be technical. Just goes to show you don't need to know much to do this fix.
Step 1
Buy stuff.
What you'll need:
1. 30W soldering iron (15W may well do)
2. Helping hands alligator clip do-dad (see picture) (optional)
3. Wrist grounding strap (optional)
4. Wire cutter
5. Ratchet
6. 7mm socket
7. High-tech rosin core silver bearing solder 0.6mm or 0.022" diameter
8. A tiny flat head screwdriver
9. A surface to work on
10. Desoldering braid (optional)
You ought to be able to buy everything you need (including the optional stuff) for $50-60.
Step 2
Take off the top of the washer.
This is a very easy step. First unplug the washer.
At the back of the washer are 3 7mm bolts. Using the ratchet and the 7mm socket simple unscrew them and then slide the top cover backwards and then up and off.
Step 3
Label all of the connectors to the white box you see at the back of the washer. Alternatively you can take digital photographs (don't rely on mine in case different production runs had different color coding). The point being you want to make sure you can put everything back together again.
Once labeled, remove all of the connectors being careful not to yank on them (and note from the photo below, there are some on the side as well). Some of them are held to the circuit board by means of small plastic clips and these you should lift up with your thumb or a screwdriver so you don't pull the wires right out of the connector.
Step 4
Uncouple the white box containing the circuit board you're after by using a flat head screwdriver to gently pry up the top most 3 white connectors (there are also two pegs that go through the back wall of the washer).
Once the box is removed using the screwdriver go around the box and slowly pry the small plastic clips holding the box together.
Finally take the top off the circuit board box (from this point on I used the wrist strap figuring it was better to be safe and grounded than sorry and fried).
Step 5
Remove the circuit board by using your small screwdriver to release the 3 plastic clips holding the board to the bottom of it's white home.
Step 6
Solder both sides of each connector. Now the board where I got most of the instructions suggested that you need to solder the whole rectangular connection but I just soldered the parts that looked worn (as seen in the photo with the magnifying glass).
That said, I put at least some solder on both sides of each connector. I chose not to bother with the boards' recommendations to take apart and clean the solenoids and relays - I also didn't resolder them
[UPDATE: December 12th, 2009. Well it worked until about a week ago, then I started getting the F d/l and F11 again. Decided it was time to tackle the relays. Reading the instructions on the various boards I decided J8 and K4 were the culprits. I re-soldered both sides of J8 and then resoldered ALL of the relays pins on the bottom of the board. Thrilled to say, everything seems to be working again!]
Step 7
Do everything in reverse to put it all back together again.
Step 8
Test to make sure your washer still works. To do so put the washer into its test cycle by selecting any wash setting, select DRAIN and SPIN, then select NO SPIN. Hit PREWASH four times within five seconds, and see C:00 come up on display. There are 8 different tests from C01-C08. Given that my washer worked right away, I don't know what would happen if a test failed.
Troubleshooting
If after everything, things aren't working at all you might have a solder bridge. Before I put my board back together again I used a magnifying glass to try to spy any solders that bled onto the connector adjacent. If you have one apparently using an exacto knife you ought to be able to divide the problem. Alternatively you could use a solder braid to de-solder the problem and then re-do it.
Also don't put your solder on too thick or it'll be tough putting the connectors back on once you're done.
If you can't get it working again you can still try to save some money by buying the circuit board replacement yourself and/or installing it on your own.
Contact the guys here and give them all of your information. This machine is a Kenmore branded Whirlpool so chances are so too will be the replacement part.
Links
I learned how to solder from this instructables post.
I found most of the instructions as to what to do over here via the incredible instructions of "thenotoriousflavio".
Summary
All told this took me $50 and 1 hour of work and I've never done anything remotely like this before.
Should you undertake the repair your worst case scenario is that you'll be out the $50 of materials and be stuck needing a new main control unit board just like you did before you started.
Best case scenario and you'll have saved yourself the over $500 reported to be the cost of the labor and parts of the F11 error repair - oh and the time and aggravation of having to wait as apparently the part is sold out all over the place due to the endemic nature of this problem.
UPDATES:As noted above roughly 11 months into the repair I had to resolder. Since then, error free through November 23rd, 2014 (today))
Thanks a ton for this posting. It worked great for me and the 2 hour estimate was accurate even with my slow, methodical process of doing things. Our He4t was just over 4 years old when this F11 problem occurred. A little silver-tin solder was all it cost to get back in working order, and we do 2+ loads every day with 4 kids.
ReplyDeleteGreat instructions and makes great sense, however after about 5 loads it was back to it's same tricks. I think i'll replace the damn thing this time. It appears for me that I have a relay problem as tapping on it while the relay is attempting to close will allow it to function. Problem is I can't see handing the wife a hammer and saying "just whack it here when it's acting up". I believe that everybodys problem may seem similar they all may be just a little different. I would blame this on the vibration. Thanks for the post.
ReplyDeleteGreat info. Thanks for documenting this process. Did you solder the connections on both the long and short sides of the board or just the short side only? Your photos show you magnifying the short side but before I put this board back in the machine, I'd like to know if I need to solder the long side as well. Thanks.
ReplyDeleteI soldered both.
ReplyDeleteI'm closing in on a year now error free.
I went ahead and soldered both sides although I only soldered the top of the long side (I guessed that might be good enough). After reinstalling everything, it worked! Thanks for the walkthrough. Ordinarily I would've just paid somebody to come out and fix it, but this saved me quite a bit of $$$$.
ReplyDeleteI just replaced the relays for the 2nd time on our washer. BTW, I ordered the replacements from Allied Electronics. Searching by their SKU number (8212208) or the Omron mfr part number (G5LE-1-DC12) should help find it. They were less than $2 each so I ordered a few extras for next time, because I know this !@#$% washer will be causing problems again in a year or so. Also, the washer was still giving F/DL and F/11 errors this time even after I replaced the relay(s). The contacts on one of the relays I removed were badly burned from arcing so I know that was still a necessary part of the fix. I tried cleaning and tinning the contacts on the edge of the board too, but it seems, as described in this blog post, that a bigger part of the problem was faulty original solder joints on the other relays. So, I got out my desoldering iron (Radio Shack #64-2060 Approx $10) and a 40W soldering pencil, and, one by one, removed and replaced the solder on every one of the leads on every one of the 5 relays (3 black narrow ones and 2 originally white ones). That got it working again... this time. Next time I might just have to solve these problems with a trip out to the landfill including a detour to some rural area and a final "fix" with a box or two of .223s.
ReplyDeleteHi, guys. I followed this quite closely. I tried the vaseline and it worked for a day. I finally had so many errors it would take me a week to do one load of laundry. I was searching on ebay for a used or new board and came in contact with Ed Edwards. He was selling a service to repair your board. I have had my repaired board for 3 days now and it works flawlessly. This is an exerpt from an email he sent me.
ReplyDelete"I perform several upgrades and repairs to these boards when I service them. It sounds like you've done some homework on the relays, and I would like you to know that I upgrade the relay to one rated for 60% more capacity instead of just replacing it. I do NOT put vaseline on your board, nor do I add solder to the contacts. These are not repairs, they are simply band-aids. I have repaired many of these after others have attempted to do so, and it's amazing how much misinformation is out there on the web. "
Here is his email and ebay listing.
http://cgi.ebay.com/Whirlpool-Duet-Kenmore-HE3T-CCU-Repair-For-F11-FDL-Code_W0QQitemZ230397337074QQcmdZViewItemQQptZLH_DefaultDomain_0?hash=item35a4c05df2
selling.surplus@gmail.com
Thank you very much, this is an outstanding guide. I did the solder trick to my HE3T and like you, almost exactly a year later, the FDL and F11 codes started up again. I've decided that I'm going to redo the solder, add a layer of vaseline, and either resolder or replace the relays. Only thing is, I'm not sure where the relays are. You mentioned K4, so I'm assuming that K1 (as well as K1 on the MCU board), which looks exactly the same, is also a relay, but what about the other box-like components (K3, K6, K7) on the board? Are these relays too?
ReplyDeleteTo be honest jimmunology, I can't recall anymore.
ReplyDeleteI resoldered the bottoms of the 3 black and 2 white boxlike things.
Haven't had a hiccup since.
I expect I may need to play around with everything annually, but it still beats shelling out the dough.
Yep, those were the box-like things that I was guessing were relays. I'll keep my fingers crossed and see how long this fix will last. If it breaks down again, maybe I'll have the eBay guy fix it for $80.
ReplyDeleteThat was exactly my plan had this not worked.
ReplyDeleteI wonder if it wasn't just J8 as there was some discolouration of the solder at that point. I ended up removing the solder that was there with a solder removing braid and then resoldered both sides and then all of the black and white box bits too as I didn't want to put it together and take it all apart again if J8 alone didn't work.
With 3 kids under 6 we do a heck of a lot of laundry around here and so far since the fix no error messages at likely 6 loads a week (pre refix was getting them almost every load for a few days before I found the time to resolder).
I didn't notice any burn marks or discoloration at any of the relay solder points, so I wimped out of resoldering them. Sure enough, my second load of laundry came up with an FDL error. It's been good ever since (3 loads now), but if it acts up again, I'll send it to the eBay guy or try to replace the relays myself with better ones, if I can find them.
ReplyDeleteWell, I found some info on another site regarding a higher rating relay (G5LE-1-E 12VDC), so I went ahead and replaced the two white relays K1 and K4. It's only been 4 loads so far, but no errors. Here's a link to that blog:
ReplyDeletehttp://www.flickr.com/photos/mysteryonionpatch/471156850
After doing some extensive reading and research I guess I should consider myself fortunate. We have had our HE4 for almost 5 years. This past weekend it threw the F/DL error and would not start.
ReplyDeleteI consulted our local appliance repair shop and they said to replace the door lock. Should be here today. I did not the F/11 code only the F/DL.
But in doing my reading I'm seeing that the CCU might be the culprit.
I have extensive training and experience in soldering and all the tools, so this might be fun.
Great post and thanks for the info.
A pleasure Butch, and please if when you're fixing yours up you note something that folks ought to know about here, please leave a detailed comment.
ReplyDeleteThanks for your blog and detailed instructions. We got the F/11 codes after we first bought our washer almost 5 years ago, thankfully Sears replaced that circuit board for free under warranty. It started happening again a few months ago and after reading your instructions I finally decided to try to fix it myself. I re-soldered both sides of all the connections around the two edges of the board where the plugs connect, and after not being able to finish a single load without stopping and restarting multiple times we have had NO errors.
ReplyDeleteThanks again.
Thanks for the awesome instructions.
ReplyDeleteI'm not an engineer so troubleshooting the board would have been tough for me. I fix most of my own stuff but in this case I would have just purchased a new board.
I tried to order the relays from Allied Electronics but the minimum order for them was 100. I purchased replacements from Digi-Key @ 1.82 a piece.
Since I'm going to replace the relays, I just de-soldered K4 and cleaned it. There was burning and arcing on the relay.
The connectors are keyed so unless you monkey fist them back in you can't connect them incorrectly. Take pictured though since at least on mine there are two terminals that do not have anything connected to them.
When soldering or de-soldering it is better to use a lower heat. High heat will melt insulation and can cause the PCB to delaminate. I used the 20w setting on my iron and was fine.
While I have been typing this, we have done 3 loads of wash. No I'm not that slow at typing, just kept getting interrupted. LOL
Oh and I just got an email from Digi-Key, the relays have shipped.
Had been getting F 11 errors randomly for the last couple months, but today I couldn't hit cancel and finish a load like I normally was able to. Stumbled onto this site and ironically, I had my soldering iron and solder handy from repairing a mic/headset. Soldiered both sides of each of the connections on the edge and I also removed and re-soldiered both white relay boxes. So far so good. By the way, heating the connections for the relays and then using a compressed air keyboard duster worked great for removing the old solder.
ReplyDeleteI want to buy new relays to eventually replace the 2 white ones and the 3 black ones, but I'm not sure exactly which ones I should get if I want to get better ones.
Looking at the following site: http://www.alliedelec.com/search/searchresults.aspx?Ntt=g5le&Ntk=Primary&sid=126A95889817&i=9&Pst=omron+&N=0&sw=y any suggestions on which ones I should purchase?
Sorry, not sure.
ReplyDeleteIf you figure it out, please come back and let us know in the comments.
Good luck!
Found this site and ordered the improved ones based on this guys comment:
ReplyDeletehttp://www.flickr.com/photos/mysteryonionpatch/471156850/comment72157612963044524/
Thanks so much for a very informative and helpful site! God bless the internet!
Thanks for the great step by step instructions. Was able to repair my HE3t washer that I'd been getting the dreaded F 11 message on for the past three months.
ReplyDeleteGood to know that there is a resource for these kind of problems.
STOP the insanity....that's what you're saying if you encounter the F11 and/or fDL error codes on your washer. If you're not there yet, you will be soon....
ReplyDeleteThe dreaded F11 and/or fDL codes - been there done ALL that!! Our Whirlpool DUET washer is just over 5 years. We experienced our first F11 code 6 months ago (warranty just expired what else is new?). When it first happened, I thought nothing of it - hit the cancel button and the machine reset itself. Then it happened again and again and again. Each time it happened it was more challenging to reset it. I searched for the fix on line - I should have done my research before we purchased the washer.
I was able to determine the error was stemming from the CCU board. Order a new one at over $300.00 and have the same thing happen again - I don't think so. We tried EVERYTHING suggested on multiple websites.....unplugging the washer, hitting the right upper side, checking wires, wiggling the wires, wedging things to improve contacts, soldering, re-soldering, Vaseline, changed relays....anything and everything was a temporary fix. Contact Whirlpool directly? Tried that too, they apparently don't recognize there is an issue with F11 fDL errors, "not a commonly called in concern". Really?? We started searching washers to purchase....I couldn't bare spending $$$ for another washer, but we are a busy active family with 4 kids - what are our options? Then one night after searching the websites for one last desperate attempt at salvaging our washer, I followed through on a link:
http://cgi.ebay.com/Whirlpool-Duet-Kenmore-HE3T-CCU-Repair-For-F11-FDL-Code_W0QQitemZ230397337074QQcmdZViewItemQQptZLH_DefaultDomain_0?hash=item35a4c05df2
email: selling.surplus@gmail.com
Now, I'm the biggest sceptic in the world and the most frugal consumer - really I am. I am posting my testament to this service because I've been there - frustrated, disappointed, angry. I am so pleased with the service Ed provided - from answering all my questions, to the superb job he did on the CCU. You can review all the comments posted by all his other pleased customers on eBay. I had to stand by my washer for the first 6 loads - just in case the beep beep beeps started. To my astonishment, amazement, and surprise - it never happened!! In my opinion, this is the only true fix for your F11/Fdl error!!
I never imagined in my wildest dreams ever telling anyone how happy I am to be doing my laundry again, but I really am!!
5 years he4t washer f11 codes... took cover off top of washer, banged on circuit board enclosure when acted up it with a wooden handle of a hammer for about a year then it completly stopped working replaced circuit board $216 $274 with tax and expedited delivery
ReplyDeleteTook apart the old one and could see the contacts all burned up under the white relay covers. sears service call $129, no thanks who knows what else they would want to replace.
Do it yourself and save...
If it happens again I think I will replace the relays with the bigger ones mentioned in one of the other posts
Thank you, thank you, thank you, thank you, thank you, thank you!!!! After years of this F11 code, replacing both the motor and a control board, and still getting the error - ending up with a washer that would fill but not spin - I was all set to buy a new washer tomorrow. I found this blog, printed it out, my husband followed your steps, and I am happily now doing my first load of laundry in almost 2 weeks :)
ReplyDeleteInstead of having to buy a new washer in a hurry, I will now be able to take my time and properly research, as well as save some money to buy it with.
You have truly made my day and started my New Year off with a smile instead of a groan.
May God bless you richly!
Thank you. Very helpful and informative. I am ordering the relays today. I did the resolder and it's working so far, but figure might as well get the relays and do a complete job. Thanks to everyone for their posts and added insight.
ReplyDeleteHello all, I have a Kenmore he4t (Model 11045981400) front load washer. About 3 weeks back I was unable to use the washer. I had an error "dL" displayed. After reading through this and another site, I decided to clean the contacts on the circuit board. It didn't make any difference. Then I purchased the door mount hardware to see if that was the problem. Installing a new one didn't make any difference. Finally I ordered the 5 relays the machine needed. I removed the old relays (remember this is the first time I had desoldered anything). I went with the copper mesh to remove solder. It didnt work well. Got a vaccum solder sucker and it worked very well. Installed the new relays (it was faster to solder new relays than to remove old ones). Put everything back and turned the machine ON. The door locked the way it should, a loud 'click' at the beginning of the cycle. I am extremely happy! Thanks for the blog.
ReplyDeleteI also have fought with Fll and DL error codes for years... I've always been able to bypass the codes by smacking on the top of the machine but the last couple of weeks, I was having to smack so often, my hand was sore.
ReplyDeleteI first pulled the board and took it to a friend who is an electrician... he checked it and added a little more solder in some places... it worked for two loads and then back to the same problems, but 10 fold!
I broke down and ordered new relays for the board... five of them. I got them from MOUSER ELECTRONICS... www.mouser.com. I believe all five cost me about $12.00 total - not including shipping. I pulled the old relays off last night, soldered the new relays on and put the board back in the machine and VOILA!!! I've done three loads with no problems! I'm a woman and have also never soldered anything before. It wasn't too bad! And I agree with the above post... when the door locked, it made the loud clicking right away with no delays. YAY!!!!!!!
Thank you for the very detailed information in your blog! I hope others will find it helpful.
My husband found your incredible blog entry after we were quoted a $450 "repair" (really means replace the part) for this exact issue.
ReplyDeleteApproximately $40 and one hour later, the problem seems to be solved. We are so very grateful and I am so happy not to be putting my expensive machine in the landfill. If we could buy you a fancy dinner in gratitude, we would!!
I sure wish the "repairmen" would learn to do this instead of selling people unnecessary replacement circuit boards!
Great post, I am in the automotive technical end for 38 years, nice to see someone take their time, have the same machine for 5 years now, just starting this F11 and DL codes.
ReplyDeleteThanks Eric Johnson
Thank you for the great information. I've inspected all the solder joints and they all look good. Pulled the relays, cleaned the one that was arcing and swapped them when I re-soldered them back onto the board. WORKING perfect now. I just ordered the better relays from Mouser Electronics to have on hand when this starts up again. I'll just keep them in the cupboard until I need them.
ReplyDeleteRelays are the only part of this fix I used. Not going to add solder to the connection tabs. In my case the relay is the only issue, for now.
Thanks again.
Thanks for this info! I am so happy to find an under-$12 solution. Would you mind sharing a link to the parts you ordered?
DeleteAfter being advised again by the better half that the washer was still acting up I decided to take a crack at it before calling sears. Google search brought me to this blog. Quick trip to radio shack for a soldering iron (sweet, now I have a soldering iron!) and $32 I was inside the washer. Took my time with the soldering and less than 2 hrs after opening it up I was successfully testing the washer. Can't say we're all set but it looks like this did the trick. Finding our site was an answer to prayers! Thank you so much for posting ( ESP with pictures!).
ReplyDeleteAnonymous Feb 25 2012
ReplyDeleteWe bought our machine in 8/2005. It started F11/DL code. I found you blog and showed it to my son and husband. They followed your direction and my machine is working like new. Thanks for saving us a $500 repair or buying a new machine.
Just wanted to say a big thank you for taking the time to create this pst. We too had the dreaded F11/DL code probelm. We soldered the board yestersay and so far so good!
ReplyDeleteI have constant problems with my 2004 he4t and the F11, and other F codes... I really think my machine is saying "FU"!! Just kidding!!! I am going to give this advice a chance, and go for it!! Many thanks for publishing this :)
ReplyDeleteA year ago, I was getting the dL code and read this article. I tried the fix and the machine worked great for a year. After a year, I started getting an F11 code on every load as soon as the spin cycle started.
ReplyDeleteI'm a handy guy so I decided I would modify the circuit board one more time and if it worked...great...if not, I would need replace the machine...the fix I was going to do was a premanent modification...
I removed the Circuit Board as described. I then completely removed the three snap connectors with the pink wire from board (I desoldered them). I then examined the board solder strips very closely and a saw a lot of delamination to the point where some of the strips were broken. I decided the only option was to hardwire the pink wires to the board directly. This would eliminate the issue of vibration that seemed to be causing the intermitent F11 codes.
I soldered new wires to the board through the holes in the board that were used for the connectors. I then used epoxy to secure the wires to the board around the holes where the wire went into the board. I then used a simple shielded contact strip (with 8 points) to connect the old pink wires to the new wires coming directly off the board.
This is a permanent modification. If this fails again, the circuit board will need to be replaced...or we get a new washer.
So far, the fix works. Since the wires are soldered directly to the board (i.e., not using connectors), I was able to resolder them to several points on the board. Since the wires are no longer attached to the board with connectors (now soldered directly on the board), vibration will no longer be a problem.
The whole thing took about 2 hrs...
15 min to get the washer apart and remove the board
30 min to remove the old connectors
45 min to solder new wires directly to the board and apply epoxy to the wires to hold them firmly to the board.
5 min to get the board back in place
15 min to wire the strip with the new wires and old pink wires
10 min to get the rest of the connectors reconnected and washer back together.
Don't do this unless you understand the principles of circuit board soldering and how to solder properly. Don't do this unless you are prepared to replace the CCU or the washer copletely.
Good luck.
Great advice. I had tried different remedies but this did it! I only resoldered the relay solders and tried an old electronics trick. I used a pencil eraser to clean off the copper strips that the connectors plug onto. No f11 codes since! Thank you!
ReplyDeleteI followed another blog's advice - he suspended the CCU with rubber bands, on the theory that it is the vibration that was causing the errors. I noticed that my gentle cycle worked fine, so I thought I'd try. Price was right. I used a bungee cord to suspend the CCU after removing it from the frame. Used a string (actually a piece of plastic surveyor's tape) to hold it down from hitting up against the top.
ReplyDeleteWorks perfectly now.
Did what a blogger recommended: suspend the CCU (detached from the frame) by rubber bands, or, as I did, a bungee cord. I used some plastic survey tape to hold it down from hitting the top. The idea is that vibration is the problem. Cheaper and easier than soldering & so forth, isolating the CCU worked fine for me. (I note that my Duet worked in gentle mode; that led me to suspect vibration.)
ReplyDeleteThank you for all the great visual and direct comments on this F11 error. I removed the board and polished the contacts with an abrasive pad. At first, I went from the F11 to HF code...but I followed the comments for the flow meter and pressure switch to find both in working order. That's when I removed the board again and polished the contact areas to have success!
ReplyDeleteOne note...if you take a continuity tester and let the flow meter spin from filling you can watch the pulses on the indicator light on the tester, thus proofing your flowmeter is working.
Thanks for saving me hundreds of dollars and the wait for a repairman.
Like all the rest of you, I've been frustrated for 6 months now (since we bought the house, with the He4T Washer) with the various F/11 and F/DL codes. I replaced the Door Latch and striker, which were both physically broken (probably from us slamming the door violently in frustration!), and the issue got a bit better... at least I could unlock the door! I did one load, and, with 2 minutes left, it threw the F/11 again! I was planning on buying a new board but wasn't convinced. Following from TheNotoriousFlavio's post to here, I was impressed by the logic presented, so I gave it a whirl. Thankfully, I had the soldering tools, so I had nothing to lose. I had to do it twice, as my initial soldering wasn't as uniform as it could be (thanks to my father-in-law for inspecting and pointing that out). I also heated up the solder connections on the blue thing between the white and black relays, re-soldering them, as the item wiggled a bit, signifying that the connections were loose.
ReplyDeleteWe've done 3 loads now with no issues. If the issue recurs, at least I know to look at the relays.
Thanks to all for the detailed information, especially the pics! Saved me a bundle of money, and it's really satisfying to NOT have to pay the mfr for this defective part!
Just a quick note that I replaced the relays on my control board two years ago and have not had a recurrence since. This will definitely fix the problem.
ReplyDeleteThank-you for posting this! Great visuals and directions!
ReplyDeleteI would like to help clarify that J8 is a connector, K4 is the relay.
Also, to resolder, I used a 20W iron. I just heated up every relay pin and touched it with a bit of new silver solder. There is not enough factory solder, so some must be added.
I also retinned the connector pins lightly with a touch of new solder.
This takes about a leisurely hour for an amateur.
Thanks again!
Has anyone ever contacted Whirlpool with this problem? Why should we all go through this? This is a manufacture defect and they should replace everyone's board for free! Come on, when they have business profiting off the fix? HUGE PROBLEM WHIRLPOOL!!! I will NEVER buy there products again, they don't back up there products.
ReplyDeleteTouched up the contacts and cleaned and resoldered the relays. I used emery board on the contacts, for a quick clean-up. One was burnt badly, so I swapped the relays. Also ordered replacements from Digikey (I figure they are easy to replace, so I just got direct replacements). On the second load now, and it works fine. Thanks, all!
ReplyDeleteBy the way, if your spin takes too long, cycles seem to take forever, or you sometimes get overflows, clean the filter/trap and replace the drain pump. I never knew there was a trap until I was replacing the pump, and it was filled with crap (bobby pins, coins, pins, etc.). Now the cycles are short and the draining is quick. I would have changed it years ago just for the savings in time.
Overall, I'd say these machines are more maintainable. than any I've had before. They just have some design flaws and it takes some cleverness and skill to do the repairs.
Thank you for this tutorial, really helpful.
ReplyDeleteMy original issue was the fact that the pink connector socket was soldered partially and such was moving up and down. Nothing that super glue for that and redo the solders.
Worked great for 6 months or so then again DL/F error. This time I re-lead all the connectors around the board and added some lead on the relays. Worked great but it was time consuming.
I've also noticed some ring cracks here and there and re-soldered them as well for good measure.
You really need to have a magnify to see these cracks. I used some jewelry glasses and it was quite an ant work but it seems like it paid off as we are back in business.
I added some dielectric grease in order to have the connectors snug and avoid arcing on the pink connectors. Also I cleaned up the entire board with some electronic cleaner and gave it a good blow with air compressor.
Hopefully it'll be good for a while otherwise I believe my next step will be to changes the relays. If so, I believe I'll need 2*G5LE-1-E DC12 and 3*Z2924-ND @ http://www.digikey.com/
If somebody can confirm?
Enjoy!
HE3T:
ReplyDeleteWe began getting the F11 code about a week ago. However, ours was different than most of the F11 horror stories. Our code came a short time after starting the machine (10-20 seconds after cycle starting), the water would start, relays would click, door locks, etc, however, the drum never turns. I read most of the F11 postings I could find (one site had hundreds of posts on it). Proactively I removed the CCU board, carefully marking the location of each wire connector, taking photos, etc. I removed the white relays from the board, swapped them, resoldered them, checked/cleaned/renewed the solder on several other relays and a few components that were less than acceptable in my opinion. However, this did not rectify my F11 issue. I then found the documentation that was once in the washer, and that the previous homeowner had removed, and ran the diagnostic test. It would not go past step C1. HMMMMMMM, back to the internet. In the literally hundreds of postings that I read through, collecting notes on a legal pad for future consideration, I did find in two or three postings that the timing of the F11 code seems to be a critical troubleshooting observation. Most F11 codes are later in the cycle, when the drum is turning, either agitating the drum, or spinning, and the vibration of this action causes the bad solder/poor relay contact issues to cause the F11 code. HOWEVER, in those two or three postings I did identify that if the code was thrown early in the cycle, as ours did, then it was a MCU issue. So, I did my parts research, identified the correct part number using the manufacturers website, then went other places to price the part. I ordered my MCU from AppplianceCentral, and the part arrived in three days. I swapped the MCU out last night, I replaced the CCU cover and snapped the CCU back in place, checked all the connections to make sure they were all seated in their sockets, and ran a load. Voila, no F11 code. I do want to thank everyone for taking their time and posting all their trials and tribulations, as well as their victories. Oh, and a quick thanks to Al Gore, without him, we'd have no internet! (haha).
HE3T:
ReplyDeleteWe began getting the F11 code about a week ago. However, ours was different than most of the F11 horror stories. Our code came a short time after starting the machine (10-20 seconds after cycle starting), the water would start, relays would click, door locks, etc, however, the drum never turns. I read most of the F11 postings I could find (one site had hundreds of posts on it). Proactively I removed the CCU board, carefully marking the location of each wire connector, taking photos, etc. I removed the white relays from the board, swapped them, resoldered them, checked/cleaned/renewed the solder on several other relays and a few components that were less than acceptable in my opinion. However, this did not rectify my F11 issue. I then found the documentation that was once in the washer, and that the previous homeowner had removed, and ran the diagnostic test. It would not go past step C1. HMMMMMMM, back to the internet. In the literally hundreds of postings that I read through, collecting notes on a legal pad for future consideration, I did find in two or three postings that the timing of the F11 code seems to be a critical troubleshooting observation. Most F11 codes are later in the cycle, when the drum is turning, either agitating the drum, or spinning, and the vibration of this action causes the bad solder/poor relay contact issues to cause the F11 code. HOWEVER, in those two or three postings I did identify that if the code was thrown early in the cycle, as ours did, then it was a MCU issue. So, I did my parts research, identified the correct part number using the manufacturers website, then went other places to price the part. I ordered my MCU from AppplianceCentral, and the part arrived in three days. I swapped the MCU out last night, I replaced the CCU cover and snapped the CCU back in place, checked all the connections to make sure they were all seated in their sockets, and ran a load. Voila, no F11 code. I do want to thank everyone for taking their time and posting all their trials and tribulations, as well as their victories. Oh, and a quick thanks to Al Gore, without him, we'd have no internet! (haha).
HE3T:
ReplyDeleteWe began getting the F11 code about a week ago. However, ours was different than most of the F11 horror stories. Our code came a short time after starting the machine (10-20 seconds after cycle starting), the water would start, relays would click, door locks, etc, however, the drum never turns. I read most of the F11 postings I could find (one site had hundreds of posts on it). Proactively I removed the CCU board, carefully marking the location of each wire connector, taking photos, etc. I removed the white relays from the board, swapped them, resoldered them, checked/cleaned/renewed the solder on several other relays and a few components that were less than acceptable in my opinion. However, this did not rectify my F11 issue. I then found the documentation that was once in the washer, and that the previous homeowner had removed, and ran the diagnostic test. It would not go past step C1. HMMMMMMM, back to the internet. In the literally hundreds of postings that I read through, collecting notes on a legal pad for future consideration, I did find in two or three postings that the timing of the F11 code seems to be a critical troubleshooting observation. Most F11 codes are later in the cycle, when the drum is turning, either agitating the drum, or spinning, and the vibration of this action causes the bad solder/poor relay contact issues to cause the F11 code. HOWEVER, in those two or three postings I did identify that if the code was thrown early in the cycle, as ours did, then it was a MCU issue. So, I did my parts research, identified the correct part number using the manufacturers website, then went other places to price the part. I ordered my MCU from AppplianceCentral, and the part arrived in three days. I swapped the MCU out last night, I replaced the CCU cover and snapped the CCU back in place, checked all the connections to make sure they were all seated in their sockets, and ran a load. Voila, no F11 code. I do want to thank everyone for taking their time and posting all their trials and tribulations, as well as their victories. Oh, and a quick thanks to Al Gore, without him, we'd have no internet! (haha).
I have sent out my board to Circuit Board Medics, but I have a question regarding the wires. I have broken one of the tabs on the 3 wire harness that goes from the CCU to the MCU. It appears there are contacts on the bottom and top so as long as one is still touching the board I should be good. Can anyone confirm this? Thanks
ReplyDelete